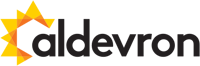
Aldevron Case Study - Microsoft Dynamics AX
Aldevron is a global biologics manufacturer of plasmid DNA, proteins and mRNA. They support companies from the research and pre-clinical testing ...
© 2025 RF-SMART. All rights reserved. Privacy Policy