Warehouse Picking Software Guide
Order picking (the process of selecting and retrieving products from warehouse storage to fulfill orders) is a critical warehouse operation. Implementing optimized picking strategies can significantly boost productivity, accuracy, and customer satisfaction. This guide explores popular warehouse picking techniques that leverage both processes and technology to maximize efficiency.
-Jun-19-2024-08-19-17-4531-PM.jpg?width=1920&height=1080&name=Color%20Backgrounds%20(1)-Jun-19-2024-08-19-17-4531-PM.jpg)
What is Warehouse Picking Software?
Warehouse picking software directs warehouse workers to the correct storage locations to retrieve items to fulfill orders. Major warehouse picking strategies include single order picking, batch picking, consolidated picking, zone picking, and automated picking.
Mobile Picking Processes in Warehouse Operations
Warehouses face a variety of options when choosing a picking method, each with their own advantages and disadvantages tailored to specific operational requirements. The right solution depends on factors including:
• Product range• Order volume and frequency
• Staff resources, and facility layout
For those with manual picking processes, the possibility of shipping wrong items and human error can significantly slow down warehouse operations and throughput.
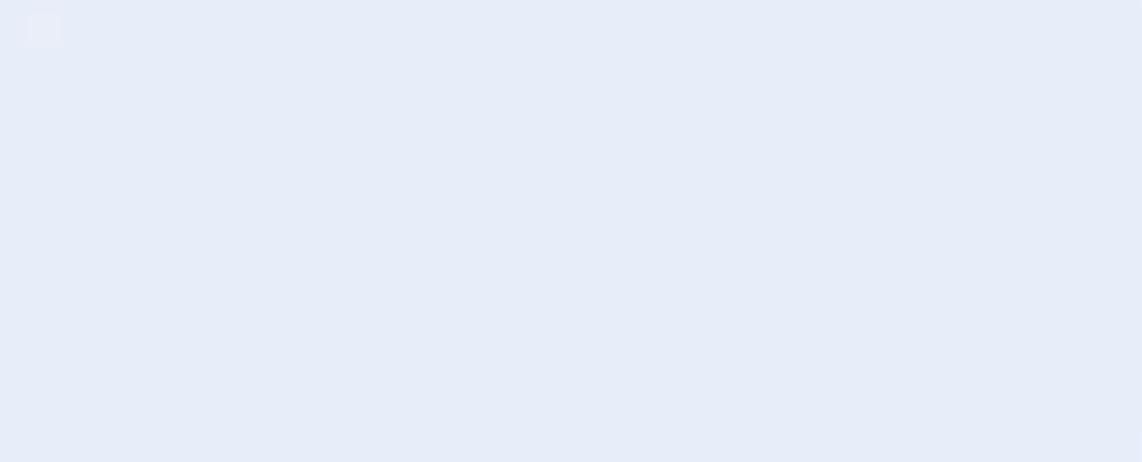
Single Order Picking
The most prevalent warehouse picking method is single order picking, where warehouse workers fulfill just one order at a time. While simple to execute, this approach can involve redundant travel throughout the warehouse to collect items.
When your picking becomes accurate, you become much more efficient.”
– Frescobol Carioca
Batch Picking
Batch picking aims to consolidate efforts by having workers simultaneously pick multiple orders, grouping by product proximity or other attributes. This allows pickers to minimize unproductive walking between picks. Batch picking works well for facilities that process high volumes of small, repetitive orders.
RF-SMART gave us the functionality we needed, including wave picking and batch picking. We chose RF-SMART because it was feature-complete for our needs." – GEM Products
Tote picking
Tote picking is an order fulfillment method where pickers place items for multiple orders into the same tote or bin during the picking process. Once picking is complete, the items are sorted out of the shared totes and into their individual orders. Tote picking increases efficiency by allowing pickers to collect items for several orders at once rather than sequentially picking orders.

Before RF-SMART, we were printing everything on paper. We were printing picking tickets, which we would give out individually to pickers and packers.” – PetShop.co.uk
Zone Picking
Another smart picking strategy is zone picking, where the warehouse gets logically divided into zones and pickers only fulfill orders within their assigned area during a wave. This segmentation limits worker congestion and reduces potential bottlenecks during peak periods. Consolidated picking takes a similar approach, clustering orders in a wave by common or nearby items to reduce travel distance.
We wanted to improve our picking, packing, and stock control with the use of a WMS. We talked to a few NetSuite partners, and all of them said ‘You must go with RF-SMART.’” - Arbortec/Flexion Global
Automated Warehouse Picking Systems
Automated picking leverages various technologies to enhance warehouse efficiency. This includes two main approaches: Goods-to-Person (GTP) and Person-to-Goods (PTG).
In GTP systems, automated technology like Automated Storage and Retrieval Systems (ASRS) bring inventory items directly to stationary pickers. Inventory can be automatically delivered via various methods including trays, carousels, totes, or robotic shuttles. Products are delivered to picking stations, reducing walking time, maximizing warehouse space, and increasing efficiency.
Conversely, PTG is a method in which pickers are aided by Autonomous Mobile Robots (AMRs) which minimize the movement required by human workers.
While automated warehouse picking requires upfront investment, it significantly boosts throughput, accuracy, and productivity compared to manual approaches, making it an increasingly popular choice for modern warehouses.
Sleepcorp’s Automated Picking
- Increase in daily picks
- Improved labor efficiency and output
- Reduced manual picking
- Streamlined picking and putaway
"By adding AMR and RF-SMART, we increased our daily picking by 65%. It’s amazing.”
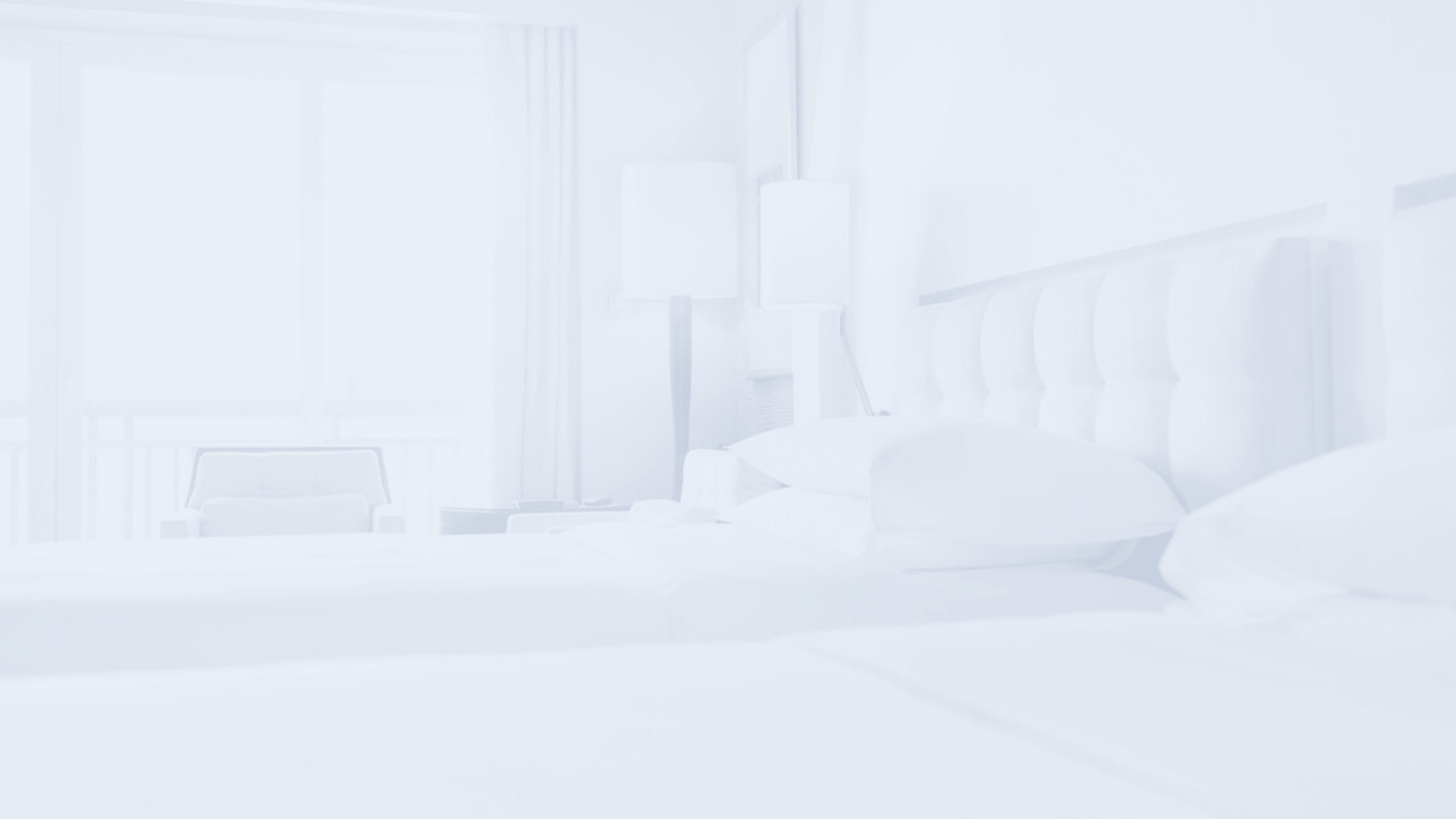
Calculate Your Picking ROI with RF-SMART
Material Handling Automation Connector
Considering adding automation warehouse management software to your warehouse?
RF-SMART offers a wide range of material handling connectors designed to integrate with our smart warehouse solutions. Our intelligent connectors allow Automated Storage and Retrieval Systems, Autonomous Mobile Robots and conveyance systems to interoperate seamlessly. This enables efficient routing and movement of inventory items to optimize fulfillment workflows. The RF-SMART Material Handling Automation Connector features robust construction, flexible configurations, and smart controls for responsive material routing.
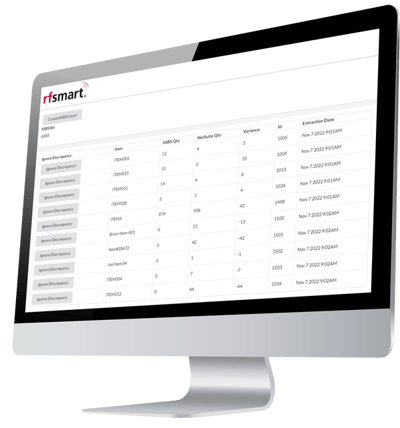
.png?width=1920&height=1080&name=Color%20Backgrounds%20(7).png)
Choosing the Right Picking Software for Your Warehouse
When evaluating warehouse picking software, key selection criteria include:
• Real-time visibility and tracking
• Flexibility to support multiple picking methods
• Analytics
• Robust integration with an ERP platform
• Scalability to grow with operations
By optimizing picking strategies and technologies, modern warehouses can achieve dramatic gains in efficiency, order accuracy, and customer satisfaction through faster fulfillment. RF-SMART goes beyond basic warehouse management to provide advanced functionality. Our solutions operate in real-time to intelligently route orders and maximize productivity.
To evaluate your warehouse’s specific needs, consider the following questions:
Do pickers walk inefficient routes through the warehouse when picking?
Would it be helpful if the picking manager was able to spend less time managing pickers and pick tickets?
Is the picking error rate below the acceptable threshold?
Do current picking methods help meet the daily order fulfillment criteria?
If yes, RF-SMART’s Picking calculator can help you identify cost-saving and ROI boosting picking solutions.
How to Improve Warehouse Picking with Wave Functionality
Efficient order picking is vital for prompt order shipping, and RF-SMART aids in this with Advanced Picking functionality. RF-SMART offers two innovative solutions to optimize how picks are organized. Pick Manager allows the warehouse manager to batch or release individual orders by selecting specific orders based on specified criteria that will provide efficiency for the picker(s). Pick Planner removes the manual process of releasing orders by creating picking strategies, such as zone or wave picking, to automatically release picking work to the warehouse based on a schedule. The output of both Pick Manager and Pick Planner is a task that removes the complexities of picking strategies from the picker.
Pick Manager
Accurate picking is the key to a fast order fulfillment process, and RF‑SMART Pick Manager streamlines this process. Our solution analyzes past picking data, real-time orders, and product availability to intelligently assign batches, routes, and sequences to pickers.
To create a faster order fulfillment process, properly organizing, assigning, and prioritizing your picks are important. Whether you need to group picks by zone or product type, or prioritize picks by shipping method, Pick Manager gives you the ability to sort through your orders electronically and release them in a way that can create efficiency for your operations.
Key features include: |
Unlike manual routing and batching, RF-SMART Pick Manager provides the ability to plan how orders are grouped and released for the pickers. An additional benefit is that Pick Manager provides bin-level allocation of inventory to prevent multiple pickers trying to compete for the same item quantities at the bin level in your warehouse.
Pick Planner
RF-SMART Pick Planner brings advanced optimization to pick planning and labor management. Our forecasting and planning engine analyzes historical orders, seasonal trends, promotions and other factors to accurately predict picking workload.
RF-SMART's Pick Planner provides the same advanced capabilities as Pick Manager, with the addition of a few more benefits.
Key features include: |
RF-SMART Pick Planner provides guidance for the best resource plans to meet demand, reduce labor spend and avoid out-of-stocks. It gives managers crucial insights into upcoming picking needs so they can optimize staffing, inventory and equipment.
Revolutionizing Warehouse Picking
Whether you're managing a small warehouse or a large distribution center, implementing the right picking strategy and software solution can transform your operations. This guide has explored various picking strategies, from traditional methods like single order and batch picking to automated warehouse picking systems and software solutions. RF-SMART's innovative offerings, including Pick Manager and Pick Planner, provide powerful tools to streamline and optimize picking operations.
-2-1.jpeg?width=1200&height=677&name=Color%20Backgrounds%20(1)-2-1.jpeg)