Warehouse Shipping
THE DEFINITIVE GUIDE
Customer expectations on warehouse shipping quality and speed are higher than ever before. The “instant” delivery model is becoming more widely offered and affordable for consumers.
In this guide, you'll learn how warehouse managers can improve shipping processes to meet customer expectations while maintaining affordable shipping rates.
.jpg?width=1920&height=1080&name=Color%20Backgrounds%20(1).jpg)
What is the warehouse shipping process?
Shipping is the final part of the warehouse fulfillment process. At this point of the inventory life cycle, the product has been received, put away, picked, and is ready to send off to the end-user. Shipping is the final touch point for warehouse staff before the customer receives the products/ expected goods. For this reason, it is vital that this process is streamlined for maximum accuracy to ensure a high-quality customer experience.
That is why in this guide we will talk briefly about what happens before packing and shipping, then focus on the process of packing and shipping itself.
Why is the warehouse shipping process important?
Businesses must be strategic in balancing customer expectations and fiscal demands when choosing their shipping rates and their shipping process.
A strong shipping process will:
- Save your warehouse time
- Reduce costs associated with shipping
- Set your business apart with faster fulfillments
- Prepare your business to scale
When something is ready to ship it typically has already gone through receiving, put away, and picking. The process of shipping is the final part of the warehouse fulfillment process.
Shipping is the final touch point for warehouse staff before the customer receives the products/ expected goods. For this reason, it is vital that this process is streamlined for maximum accuracy to ensure a high-quality customer experience.
How accurate should my shipping process be?
To keep your warehouse running at peak efficiency it’s important to evaluate industry productivity metrics to prioritize your technical investments. According to WERC, a professional organization devoted to warehousing and supply chain, there are a few key performance indicators that can help you determine areas of improvement for your fulfillment process:
Shipping Process: How do I Measure Customer Experience?
The metrics below encourage greater customer retention & satisfaction.
On-time shipments: Are your shipments leaving your warehouse in a timely manner? On-time shipments is a calculation of the percentage of shipments that arrived at their destination on-time. Best-in-class average is 99.5 percent and above.
- On-time shipments = Number of orders shipped on-time/Total number of orders shipped X 100
Percent of orders with on-time delivery: Did your shipment arrive to your customers within the agreed-upon timeframe or within their SLA requirements? Percent of orders with on-time delivery is the overall percentage of total shipped orders that arrived on-time. Best-in-class average is 99 percent and above.
- Shipments with on-time delivery = Number of orders that arrived on-time/Total number of orders shipped X 100
Shipped complete per customer order: Did the order get shipping completely and accurately? Shipped complete per customer order is the percentage of shipments where all order components ship and arrive at the same time. Best-in-class average percentage is 99 percent and above.
- Shipped complete per customer order = Number of orders components arrived on-time/Total number of orders shipped X 100
Shipped damage-free: Were items in the shipment packaged properly to ensure safe shipping and handling? Shipped damage-free is a calculation of shipments that arrived at their destination in an undamaged state. Best-in-class average percentage is 99.4 percent and above.
- Shipped damage free = Number of orders shipped damage free/Total number of orders shipped X 100
Measuring Shipping Operational Success
Below metrics directly correlate with inventory production, management, and control.
Distribution cost per unit shipped: Do you know how much shipping this order is costing your business? Distribution cost per unit shipping is the average cost for shipping/distributing a unit of product. Best-in-class operations have less than $0.50 average cost.
- Distribution cost per unit shipped = Total distribution costs/Total number of orders shipped
Orders picked and shipped per hour: How many orders are getting out the door per hour? Orders picked and shipped per hour is the number of orders shipped in one hour of production. Best-in-class number is 67 or more per hour.
- Orders picker per hour = Total orders picked and shipped/Total hours worked in picking
Distribution costs as a percentage of goods sold: Do the total costs to ship align with the budget of your business? Distribution cost as a percentage of goods sold is the total distribution expenses divided by the total cost of goods sold. Best-in-class percentage is less than 2.76 percent.
- Distribution cost as a percentage of goods sold = Total distribution costs/Total number of orders shipped x 100
All the metrics above can be addressed by prioritizing speed and accuracy from picking to shipping, while also choosing the best rate for each shipment based on the customer SLA. To accomplish this, investing in capable shipping software can improve these metrics and track consistent progress.
How do You Get ROI with RF-SMART Shipping?
Try our ROI Calculators to Find Out!
Pre-Shipping Process
Receiving & Putaway
Each warehouse has its own supply chain receiving and putaway process to input and organize inventory in their warehouse. In this part of the process, products are input into the system of record and taken to either reserve or active inventory locations/bins for eventual picking.
Before a shipment can take place, the warehouse’s system of record must receive the customer order. This will inform the necessary data needed to pull the order, including:
- Product names
- Quantities
- Delivery address
- Expected delivery date range
From there, the order will trigger the warehouse team to begin preparing for the shipment, starting with picking the ordered products.
Inventory Picking
For each order, the warehouse team will be assigned a picking order to secure the necessary products for the shipment.
Although a wide array of picking processes exist, the most common include case picking*, discreet picking*, and batch picking*. Those interested in enhancing the process may choose to add material handling equipment or other automation.
It is crucial that warehouse managers have live access to the available inventory through a strong inventory management software solution. Otherwise orders can be delayed due to missing inventory.
Once picked, these items will be taken to the shipping station and the pre-shipping process is complete.
*Case Picking: Requires warehouse pickers to pick full cartons, boxes, or cases of product, rather than picking items by eaches. This method is commonly used for warehouses with high quantity orders.
*Discrete Picking: Warehouse pickers picks one order at a time, guided through the order by line items. This is most common for warehouses using paper-based picking.
*Batch Picking: Multiple orders are picked at once, grouped by location in the warehouse. This method requires picking logic to help organize orders by bin location.
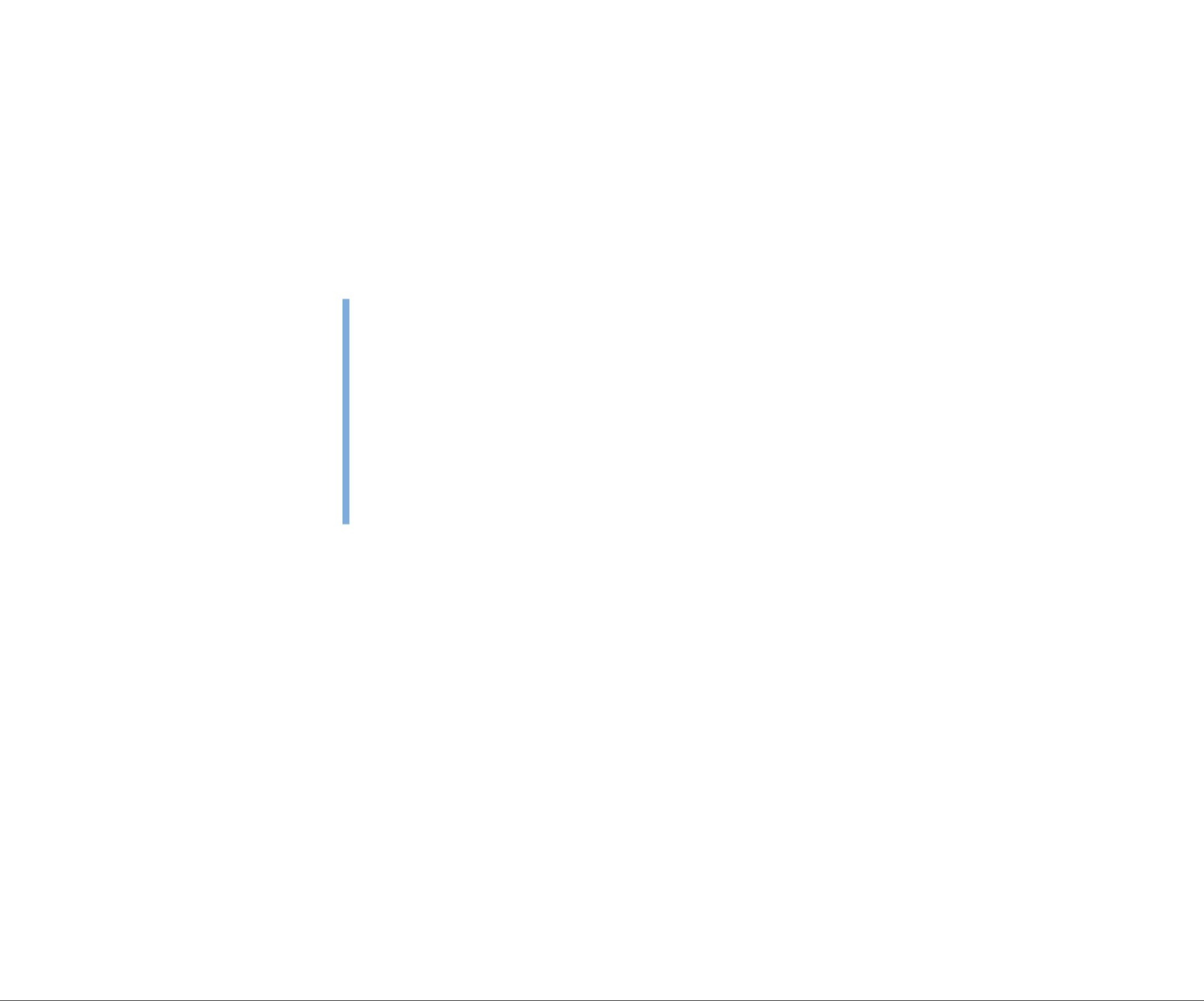
PRO TIP: Getting ROI out of Shipping
Reducing storage and retrieval inefficiencies can significantly reduce the costs of warehouse operations. It is estimated that about 50% of labor in a warehouse results from picking, packing and shipping.
Check out this WMS ROI calculator to see how much your warehouse might be able to save by optimizing.
Shipping Process
Pack
Once the ordered items arrive at the shipping station, the first step is to ensure all items are packed properly. Packing may be done in early parts of the inventory process, depending on each warehouses’ specific process. Some warehouses choose to pick and pack in the same step, called pick-to-carton.
Depending on the goods, some products may need additional packing measures, including padding, temperature control, or specific configuration. The outside packing will also vary based on shipment contents. Regardless of tape and wrapping used, any special considerations need to be clearly identified on the package’s exterior. Examples include fragility, orientation, hazardous materials, etc.
Weigh & Dimension
Once the order has been prepared for delivery, the package needs to be evaluated to document weight and size. Depending on your ERP and inventory organization, weighing the package may not be necessary. If weights and measurements already exist inside your system of record you may not need to weigh the items.
There are various weight and dimensioning tools available to expedite this process. Depending on the average parcel size and configuration, a desktop scale may be appropriate, or a large scale may be required.
For dimensioning, handheld scanners are available to dimension and update product measurements as they are received into the warehouse.
Rate Shop/Choose Carrier Service
As with any step in the shipping process, carrier service options and rates may vary.
This step must include:
- Checking the order information to determine if expedited shipping is necessary
- Keeping carrier decisions in accordance with the customer’s SLA
- Address any other special considerations
- Account for those special considerations
- Notating special considerations properly
Print Shipping Labels
Once the carrier service is selected, printing and attaching a shipping label is the next step. Label printing can be configured in various ways to accommodate product needs.
Most often this includes a desktop printer that quickly prints labels directly after rate shopping. From there, this needs to be attached to the outside of the shipment.
Print Shipping Documents
Each shipment will have its own set up necessary shipping documents that need to be included. To note, these could potentially be included in the packing stage, depending on how the shipments are packaged.
Potential documents include Customer Receipt, Authenticity Certificate, Waybill, Packing Slip, and Unpacking Note. For international shipments, more documents may be required depending on the country of origin and the destination country.
Ship
This is the final step of the fulfillment process. It is also the last touch point before the product is officially out of the company’s custody.
The product will be moved to the shipping area to be properly distributed to the correct carrier at the shipping dock. Depending on product size and warehouse layout, package movement from shipping station to shipping dock will vary per location.
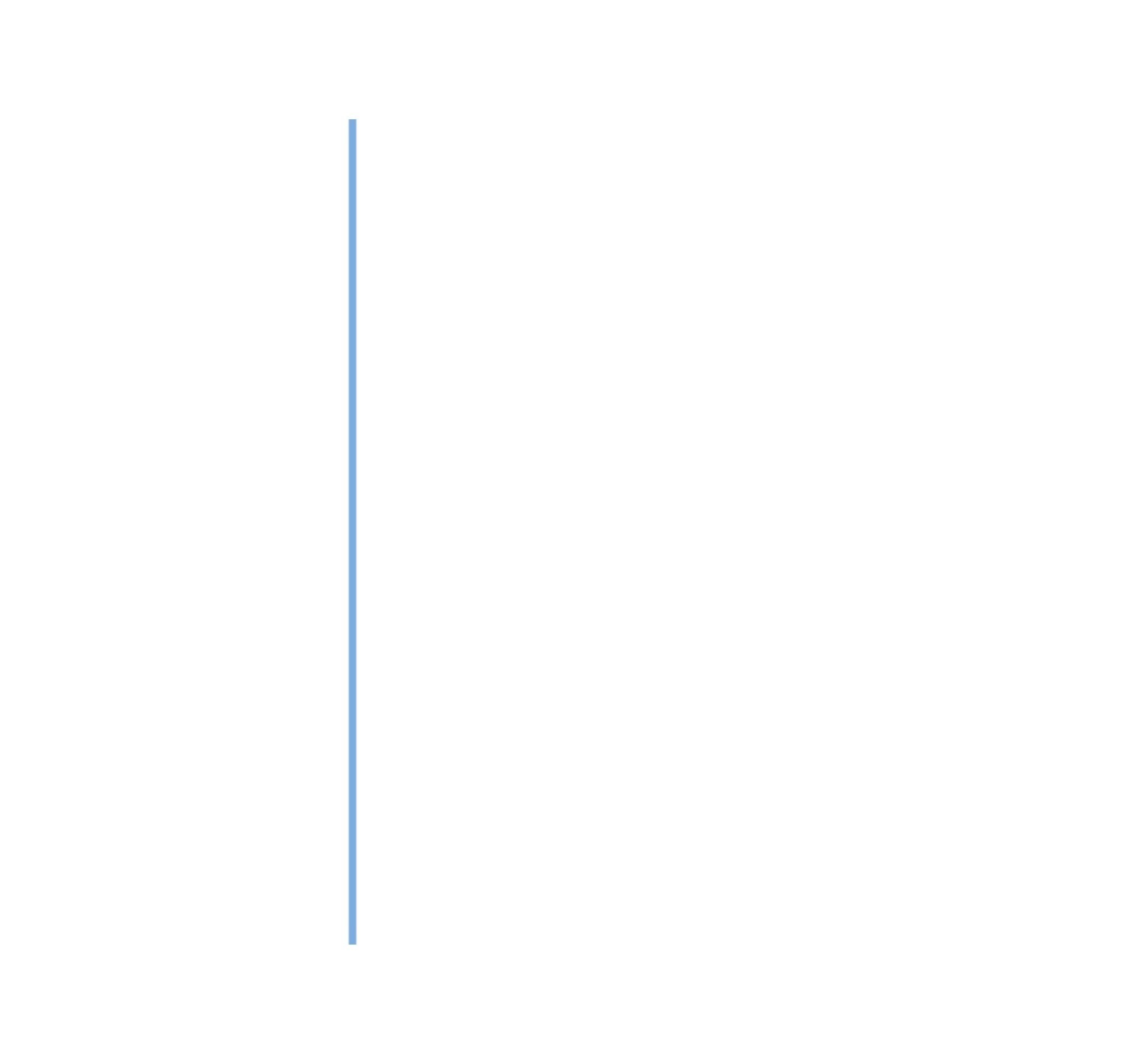
Post-Shipping Process
Post shipping is sure to be the most flexible of all fulfillment’s steps. It tends to vary greatly depending on company structure, customer service expectations, and product type.
Tracking
With each shipment, tracking is necessary to ensure customer satisfaction and reduce fiscal impact resulting from lost shipments. Having a system of record that notates product location is crucial, especially when customers will be updated about tracking information.
A capable shipping software will allow customer service to have access to the tracking information produced during shipping in real-time.
Reporting
Review As with any warehouse process, aggregating and reviewing available shipping data is crucial. Each warehouse should have a clear view of their overall shipping statistics, including common shipment size, shipment cost, package size, etc.
This allows the warehouse buyers to make better purchasing decisions and leverage carrier data to negotiate better pricing.
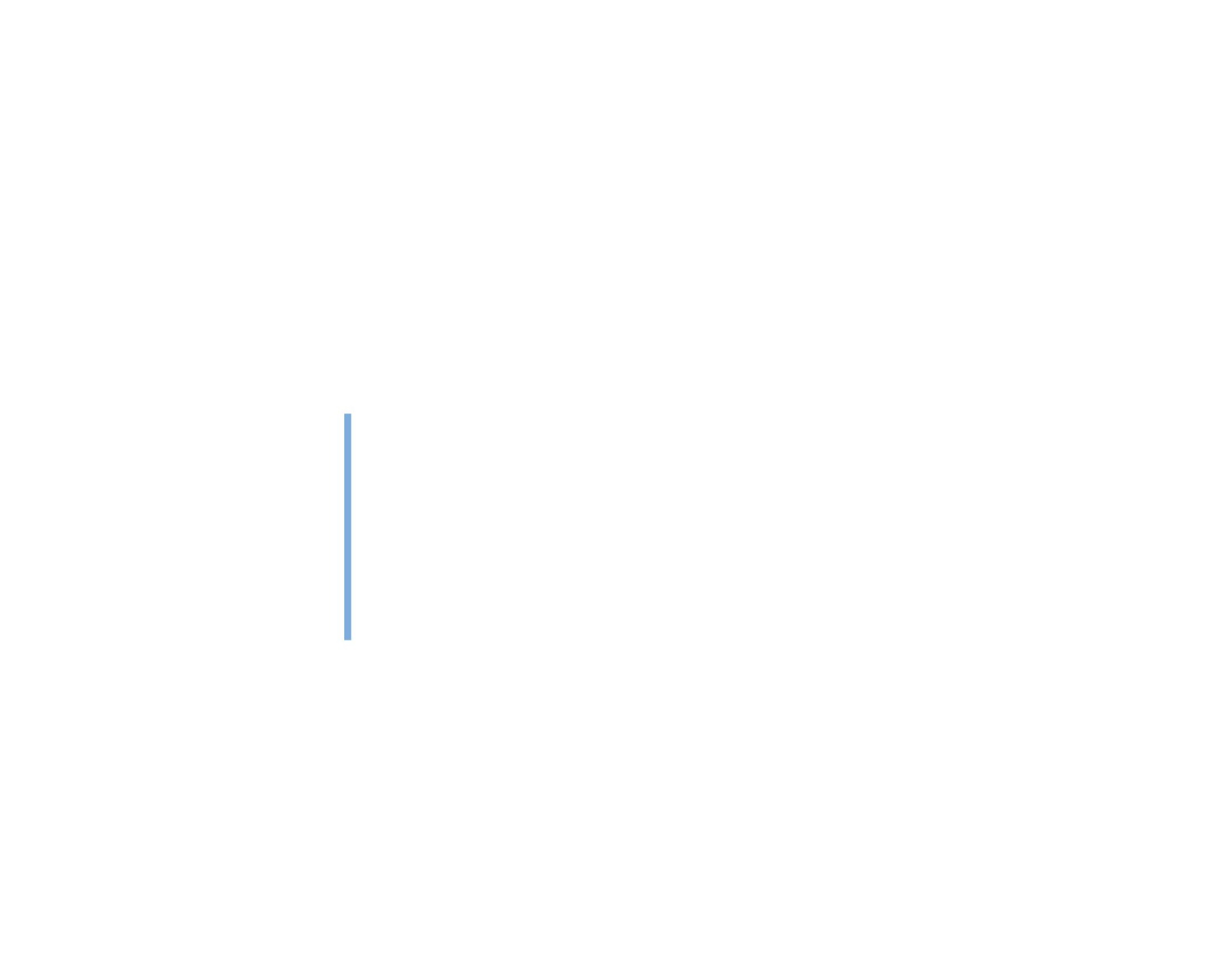
How can I decrease the number of manual steps in our shipping process?
This challenge can be eliminated by investing in software that uses barcode scanning to guide shippers through the process. This eliminates manual keying in of data, speeds up the shipping process, and reduces human errors.
How many user interfaces (UIs) should I need to engage with to ship one product?
One. Your shipping software should operate on one user-friendly UI. This eliminates the need to toggle back and forth between your shipping software and carrier system for each fulfillment. Evaluating different solutions and determining which can accommodate this need is key.
How can I get warehouse staff to rely on best practices and not posted sticky note rules/individual knowledge?
A shipping platform should have stringent built-in guidelines. With this type of guided solution, warehouse staff will be taken through a defined process that is faster and more accurate.
Relying on sticky notes or other more manual processes for shipping guidelines typically:
- Slows down the shipping process significantly
- Causes violations of carrier rules (which often means extra charges or a package not shipping)
- Wrong package sizes
- Selecting the wrong rates for the delivery needs of the package
A well-structured and fast shipping solution will typically pay for itself very quickly in a relatively busy warehouse.
Why is my shipping process so slow?
Most shipping processes are slow due to a combination of these three common challenges:
- Shippers needing to make too many decisions
- Outdated technology (5+ years old) not meant to operate in the cloud
- Too many steps in the shipping process
It is important to find a solution that can have the best accuracy in as few steps as possible.
Make sure to ask to see a live demo when evaluating a shipping software to get insight into performance.
How do I design a more sophisticated shipping carrier network strategy without forcing my shippers to be subject matter experts?
Your shipping software should allow admins to configure rules that guide warehouse staff to the best carrier choice.
This eliminates the need for warehouse shippers to make complex decisions. The software will consider custom requirements, including SLA or other customized rules.
How can I make rate shopping easier and faster?
Get a shipping software solution that has built-in automated rate shopping. This will ensure you’re getting the lowest price every time, every shipment.
Automate rate shopping capabilities including carrier and service per package, Service Level Agreement (SLA), and more. This ultimately results in saved time and money.
Customer Experience
"RF-SMART Shipping was a lifesaver during the holiday season. We timed our shippers, and they were able to ship out packages with RF-SMART 3X faster than with our old solution. With over 3,000 packages a day, we saved over 13 hours a day in time for our business. "
SMOKY MOUNTAIN KNIFE WORKS >
Ryan Ferguson, VP
Popular Parcel Shipping Methods
Here are three popular Parcel Shipping methods:
B2C
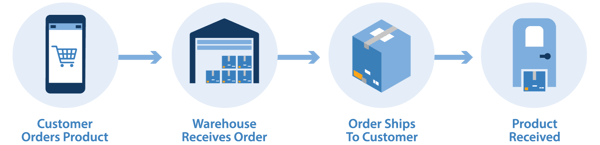
Drop Shipping
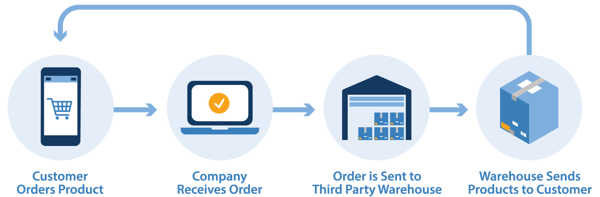
B2B / Wholesale B2B
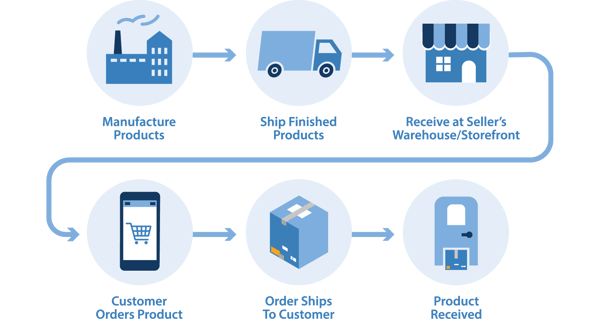
How RF-SMART Shipping for NetSuite Works
RF-SMART Shipping was built in partnership with our customers to address the common delivery challenges that our customers were facing. We created a fast, configurable, and easy-to-use solution that has maximized the shipping potential of RF-SMART’s customers.
RF-SMART
Shipping Tip
Your shipping software should be efficient and accurate, helping reduce user error. RF-SMART's Shipping ROI calculator can help you calculate potential shipping savings. This includes savings from reducing misshipments and shorter label printing times.
Customer Experience
"We are saving around $4,000 a week just by rate shopping through RF‑SMART Shipping. That does big things for my warehouse. I can give raises, I can give bonuses, just by not having to hire a ton of people.
I can add a second job function to my shippers’ day now, allowing me to get more done. I’m able to do so much more in other places in my warehouse because I know shipping is taken care of and I don’t have to worry about it."
SLATE ROCK FR >
Kayla Hill, Warehouse Manager
Quick Automated Processes
All warehouse steps lead to shipping. If this part of your supply chain isn’t streamlined, all other improvements are less impactful. A great shipping strategy should combine quality assurance with speed.
If shipping process times increase, bottlenecks arise. Often these bottlenecks cause more errors, as shippers begin to multitask while waiting for labels to print and orders to complete. This can be avoided with efficient software that implements guidelines to decrease shipping times.
If shipping productivity increases, the number of staff on the floor can decrease, saving time and labor. These resources can then be allocated for warehouse personnel and supply chain improvements, creating a healthier environment that improves employee retention and increases business efficiency.
Customized Experience
With any new shipping software, it’s crucial that the new solution recognizes your company’s specific needs and requirements. Without this, many steps of the shipping process are bound to be manual and tedious, making up for the gaps where the software doesn’t align with the warehouse systems. This ultimately results in more errors and slower shipping times.
Any shipping solution implemented should be able to function as a guide through your warehouse process. It should be able to set parameters that keep orders moving out the door accurately and efficiently. This software should continue to adapt to your growing warehouse needs and scale as products and order volume changes.
Intuitive Design
Alongside strong performance and maximum speed, great shipping software should be designed for maximum ease of use.
For shippers, the simpler the procedures, the better. This allows each team member to focus solely on the shipment itself. Otherwise time can be lost troubleshooting the technology being used to facilitate the process.
Ease-of-use should be present in all areas of the shipping experience, from software to hardware. For an optimal picking process, using scanning and minimal manual entry is ideal for reliability and accuracy.
An effective shipping solution will help minimize the number of necessary tools. This helps to keep workstations more compact and less cluttered. It is also essential that it communicates back to the system of record in real-time.
An intuitive design can also makes the training process significantly easier for seasonal hires. When adding team members in busy season, an easy-to-use system is key. This means more time can be focused on fulfillments and less on training when orders are at their peak.
Customer Experience
"Before RF-SMART Shipping, we would encounter that spinning wheel of death while waiting for the label to print. Now that’s a non-issue – this change increased our ship rate by 30%."
KIRBY ALLISON HANGER PROJECT >
Kirby Allison, CEO